The use-case of this article involves the construction of 5 towers on a 500,000m2 site. The mixed-use development will contain luxury apartments, office space, a five-star hotel and commercial retail. The project originally was assigned to another contractor prior to the involvement of CCC.
One of the most important challenges in this stage is to review the work which has been done by the previous contractor. The inspection of the existing construction helps the engineers to decide whether to carry on or to modify them.
Figure 1a: Abu Dhabi Plaza
The objective was the structural inspection of the diaphragm (Dwall) wall (figure 1) in comparison to theoretical position. In this case, the level of tolerance of the deviation from the theoretical position must be minimal since the design involves the construction of the inner wall (or parking wall), along the diaphragm wall, in a distance of 15cm. More specific, the distance between the inner side of the diaphragm wall to the outer side of the parking wall must be 15 cm, according to the design (Figure 2).
Figure 2: Diaphragm wall position in comparison with the inner wall
The high level of detail which is required cause the necessity to utilize a method which allows us to get the as-built situation as it is and to analyze into
advanced CAD/BIM system.
Figure 1b: Point clouds
Recent advances in generating 3D environments using laser scanning technologies, and acquiring quality information about built environments using embedded and other advanced sensors provide the capability to frequently gathering an integrated and accurate three-dimensional and material quality related as- built data. This information is combined with the design BIM model with an objective to create an integrated model which is dynamically updated during the construction period.
Overview of the approach - Laser Scanning Aplication
The site scanning, with the usage of the laser scanner technology, was completed in 4 days with 400 scans in total. Advanced computer software gives us the ability to generate vertical and horizontal cross section, along the diaphragm wall, allowing the user to define the interval between the consecutive cross sections. The interval of the cross sections was determined with the assistance of the project’s engineers. The decision was based on the length of the panels which constitute the diaphragm wall. Therefore, an interval of 5 meters between two consecutive cross sections allows us to check the as-built condition of every panel. The resulted cross sections highlight the parts of the wall where the deviation exceeds the critical tolerance of 15 cm from the theoretical position.
Figure 3: Image generated from the laser scanner illustrating the façade of the west section of the Dwall. Furthermore, the software allows us to generate horizontal cross section. The horizontal cross sections were generated in three elevation spots, one in the lower, one in the middle and one in the upper part of the wall. In total 150 vertical cross sections were generated and also 12 horizontal cross sections. In sectional view (figure 4) the slope of the wall and the verticality is highlighted as well as the direction of the deviation. Figure 4: Vertical cross section of the wall In the above figure, it can be seen, that the wall does not follow the verticality rules since there is a curve in the middle of the wall. In the right side of the figure 4, the as- built is represented superimposed by the design (red line), indicating the value and the direction of the deviation from the hypothetical wall position. In this example, the distance between the as-built Dwall position (white line) and the theoretical Dwall position (red line) is 25 cm, a value which violates the design specification. The figure below indicates a horizontal cross section. As it can be seen, the as-built Dwall position (white line) exceeds the theoretical position (red line) and penetrates into the boundary of parking wall (blue line).
Figure 4: Horizontal cross section
The sectional analysis cannot cover the whole surface of the wall since the as-built conditions of the areas between the intervals are unidentified. Therefore, we need an integrated project model were the deviation is depicted in the whole surface of the wall providing the value and the pattern of the deviation in every spot. found, it can be evaluated according to construction specification to define if any detected deviation violate any specification and as a result constitute a defect. The resulted model constitutes a color based deviation model, as it is indicated in the figure 5. The color is assigned according to the value of the deviation between the as-built measured data and the design model. In figure 5, the areas which are red colorized represent the highest deviation with values which exceed 150mm. In contrast with the green colorized areas that present the lowest deviation with the values which are fluctuated between 0mm to 150mm. The positive pattern of deviation is illustrated with red shades while the negative deviation with blue shades. The red colorized areas (figure 5) indicate the areas where the wall penetrates into the parking wall and therefore must be trimmed. The green areas indicate the parts of the wall where the deviation is fluctuated
Figure 5: Color based deviation model of the West section of the wall
Identification of deviation can be completed by comparing the as built data, acquired by the laser scanner, to the given design model. Once the magnitude of deviation is within acceptable limits while the blue color indicates the areas where the wall is deviated with opposite direction.
Foundation inspection The engineers also requested the inspection of the existing rafts (figure 6) which were constructed from the previous contractor. The rafts inspection involves the review of the slopes and comparison of the elevation with the design. The figure below indicates the fluctuation of the slopes of the foundation. The dark red shows the areas where the distance from the theoretical raft position exceed 10 cm while the green indicate the areas where the deviation is lower than 5mm. existing construction obey the design specification or violates them. The implementations of 3D technologies in combination with advanced software enable the engineers to locate the defects accurately and effectively. After the data acquisition stage, the as-built data are compared with the design with an objective to detect the deviations. In case, there are deviations which exceed the acceptable limits according to the specification then a further analysis is required. The quality control approaches.
Figure 6: Raft inspection
Conclusions
The utilization of laser scanner technology on construction sites can improve the as- built data collection procedure. The laser scanner technology can be used to optimize the project quality control processes since provide a detail view of the as-built situation. The engineers acquired a thorough view of the existing construction and are able to evaluate whether the which are used so far provide information only for a specific location without reflecting the pattern and the magnitude of the deviation between the as built data and the design. The current approach, employing new technologies in the field of surveying, establishes an automated procedure for extracting quality control report and provides integrated information about the status of the work on construction sites.
Autor: Amjad El-Masri
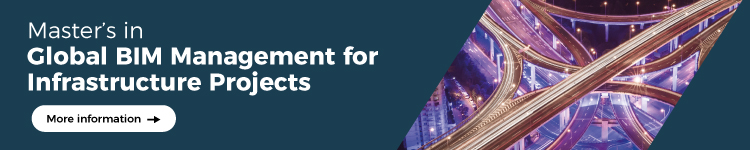